تنقسم طرق طلاء مقاوم الضوء عمومًا إلى طلاء الدوران، والطلاء بالغمس، والطلاء باللف، ومن بينها الطلاء بالدوران هو الأكثر استخدامًا. بواسطة الطلاء الدوراني، يتم تقطير مقاوم الضوء على الركيزة، ويمكن تدوير الركيزة بسرعة عالية للحصول على فيلم مقاوم للضوء. بعد ذلك، يمكن الحصول على فيلم صلب عن طريق تسخينه على طبق ساخن. يعتبر الطلاء الدوراني مناسبًا للطلاء من الأفلام الرقيقة جدًا (حوالي 20 نانومتر) إلى الأفلام السميكة التي يبلغ سمكها حوالي 100 ميكرومتر. خصائصه هي التوحيد الجيد، وسمك الفيلم الموحد بين الرقائق، وعدد قليل من العيوب، وما إلى ذلك، ويمكن الحصول على فيلم ذو أداء طلاء عالي.
عملية طلاء تدور
أثناء الطلاء بالدوران، تحدد سرعة الدوران الرئيسية للركيزة سمك طبقة مقاوم الضوء. العلاقة بين سرعة الدوران وسمك الفيلم هي كما يلي:
تدور = كيلو طن
في الصيغة، Spin هي سرعة الدوران؛ T هو سمك الفيلم. k و n ثوابت.
العوامل المؤثرة على عملية الطلاء الدوراني
على الرغم من أن سمك الفيلم يتم تحديده بواسطة سرعة الدوران الرئيسية، إلا أنه يرتبط أيضًا بدرجة حرارة الغرفة والرطوبة ولزوجة مقاوم الضوء ونوع مقاوم الضوء. تظهر المقارنة بين أنواع مختلفة من منحنيات طلاء مقاوم الضوء في الشكل 1.
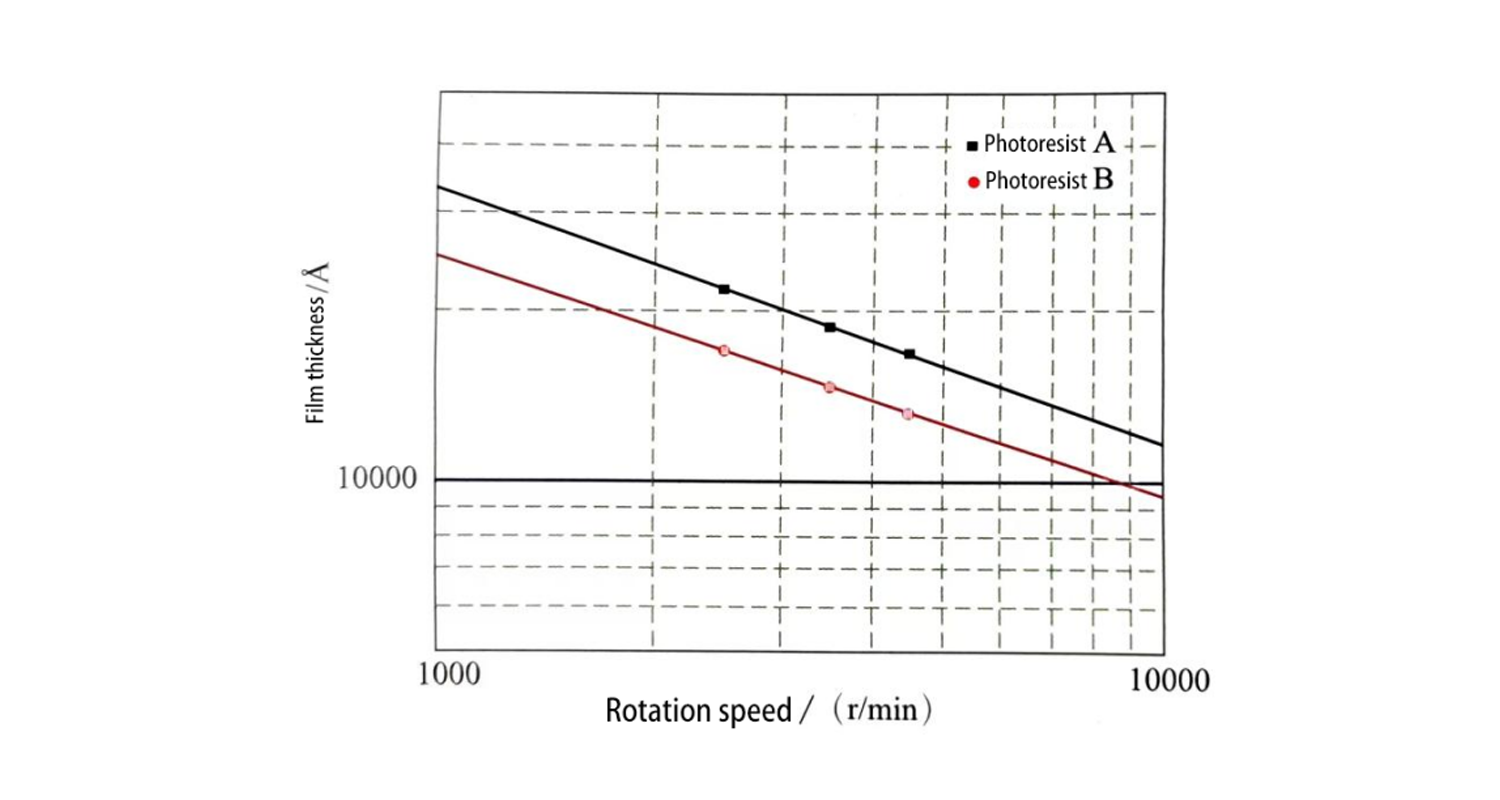
الشكل 1: مقارنة بين أنواع مختلفة من منحنيات الطلاء المقاوم للضوء
تأثير وقت الدوران الرئيسي
كلما كان وقت الدوران الرئيسي أقصر، كلما زادت سماكة الفيلم. عندما يتم زيادة وقت الدوران الرئيسي، يصبح الفيلم أرق. عندما يتجاوز 20 ثانية، يبقى سمك الفيلم دون تغيير تقريبًا. ولذلك، عادة ما يتم تحديد وقت الدوران الرئيسي ليكون أكثر من 20 ثانية. تظهر العلاقة بين وقت الدوران الرئيسي وسمك الفيلم في الشكل 2.
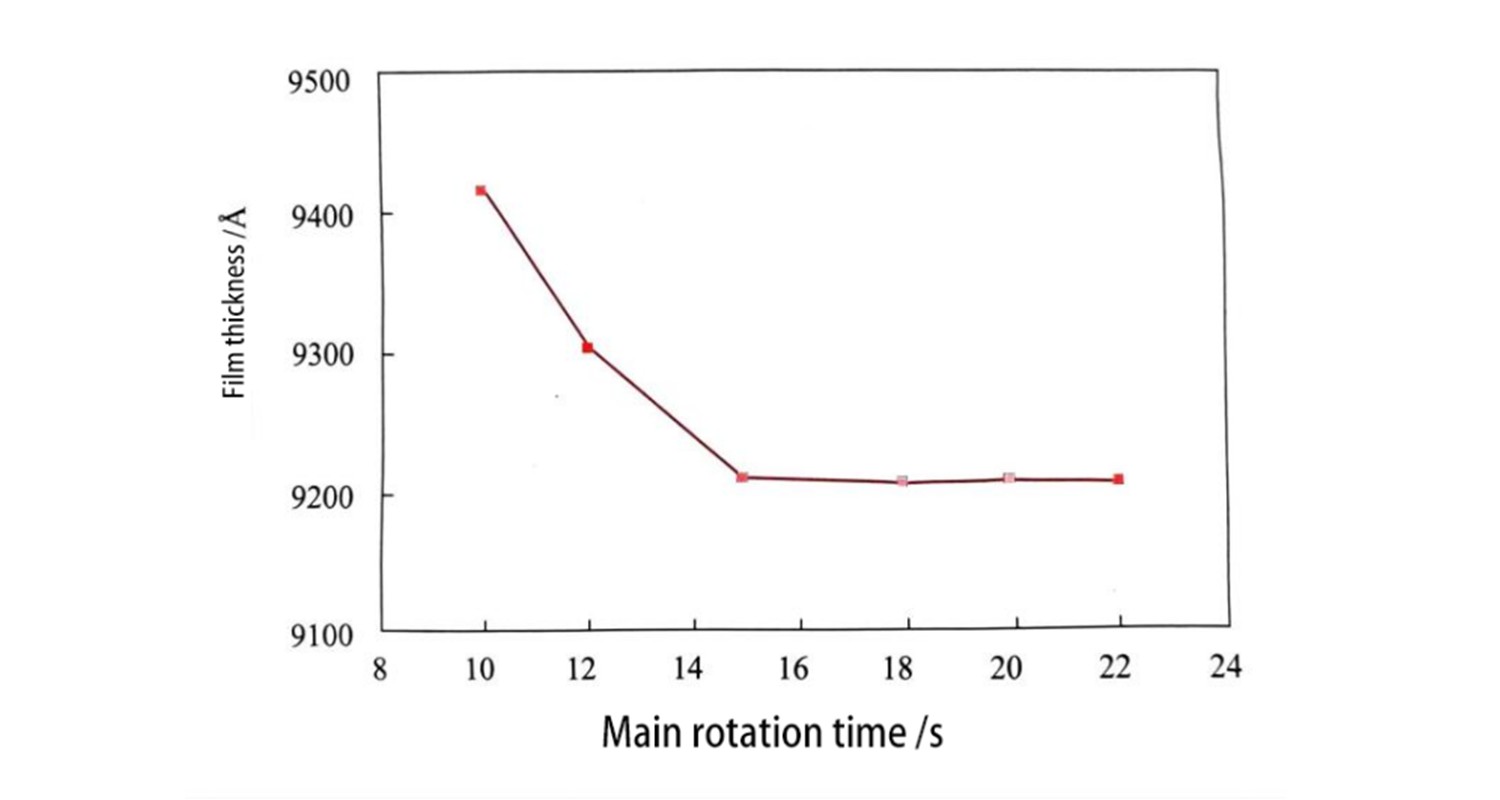
الشكل 2: العلاقة بين وقت الدوران الرئيسي وسمك الفيلم
عندما يتم تقطير مقاوم الضوء على الركيزة، حتى لو كانت سرعة الدوران الرئيسية اللاحقة هي نفسها، فإن سرعة دوران الركيزة أثناء التقطير ستؤثر على سمك الفيلم النهائي. يزداد سمك طبقة مقاوم الضوء مع زيادة سرعة دوران الركيزة أثناء التقطير، وهو ما يرجع إلى تأثير تبخر المذيب عندما يتم فرد مقاوم الضوء بعد التقطير. ويبين الشكل 3 العلاقة بين سمك الفيلم وسرعة الدوران الرئيسية بسرعات دوران الركيزة المختلفة أثناء تقطير مقاوم الضوء. يمكن أن نرى من الشكل أنه مع زيادة سرعة دوران الركيزة المتساقطة، يتغير سمك الفيلم بشكل أسرع، ويكون الفرق أكثر وضوحًا في المنطقة ذات سرعة الدوران الرئيسية المنخفضة.
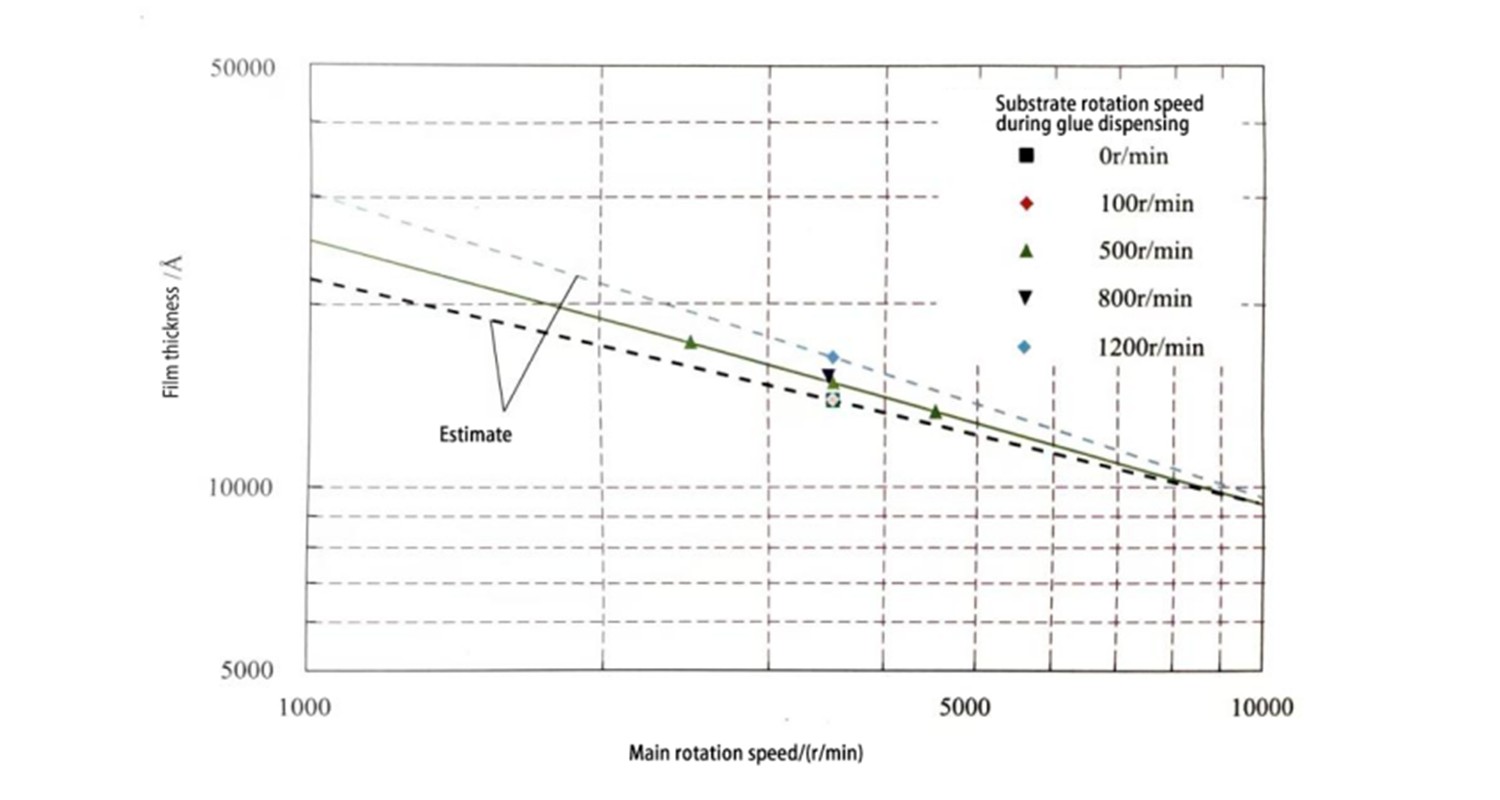
الشكل 3: العلاقة بين سمك الفيلم وسرعة الدوران الرئيسية عند سرعات دوران الركيزة المختلفة أثناء توزيع مقاوم الضوء
تأثير الرطوبة أثناء الطلاء
عندما تنخفض الرطوبة، يزداد سمك الفيلم، لأن انخفاض الرطوبة يعزز تبخر المذيب. ومع ذلك، فإن توزيع سمك الفيلم لا يتغير بشكل كبير. يوضح الشكل 4 العلاقة بين الرطوبة وتوزيع سماكة الفيلم أثناء الطلاء.
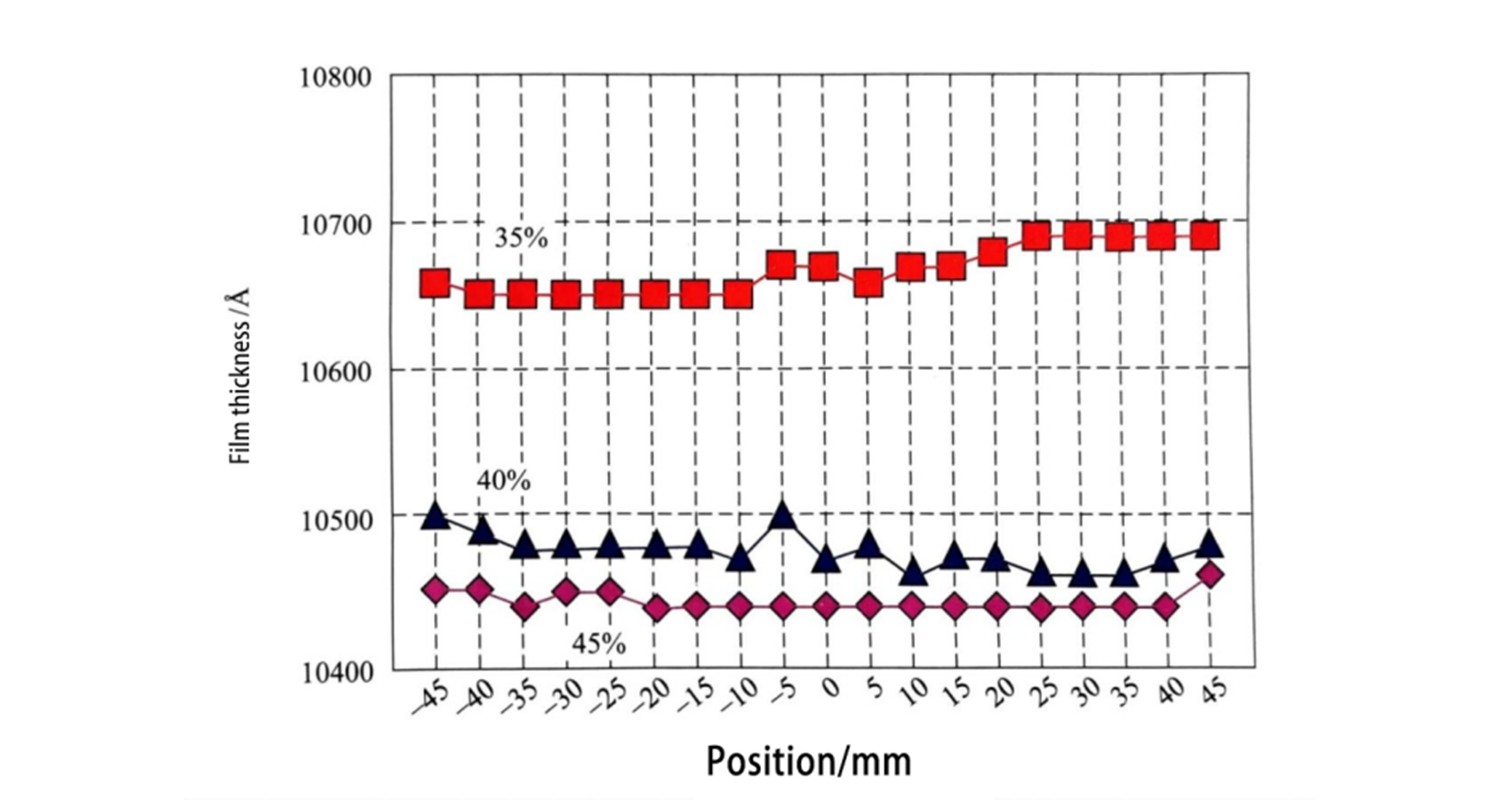
الشكل 4: العلاقة بين الرطوبة وتوزيع سماكة الفيلم أثناء الطلاء
تأثير درجة الحرارة أثناء الطلاء
عندما ترتفع درجة الحرارة الداخلية، يزيد سمك الفيلم. يمكن أن نرى من الشكل 5 أن توزيع سمك طبقة مقاومة الضوء يتغير من محدب إلى مقعر. يوضح المنحنى الموجود في الشكل أيضًا أنه يتم الحصول على أعلى تجانس عندما تكون درجة الحرارة الداخلية 26 درجة مئوية ودرجة حرارة مقاومة الضوء 21 درجة مئوية.
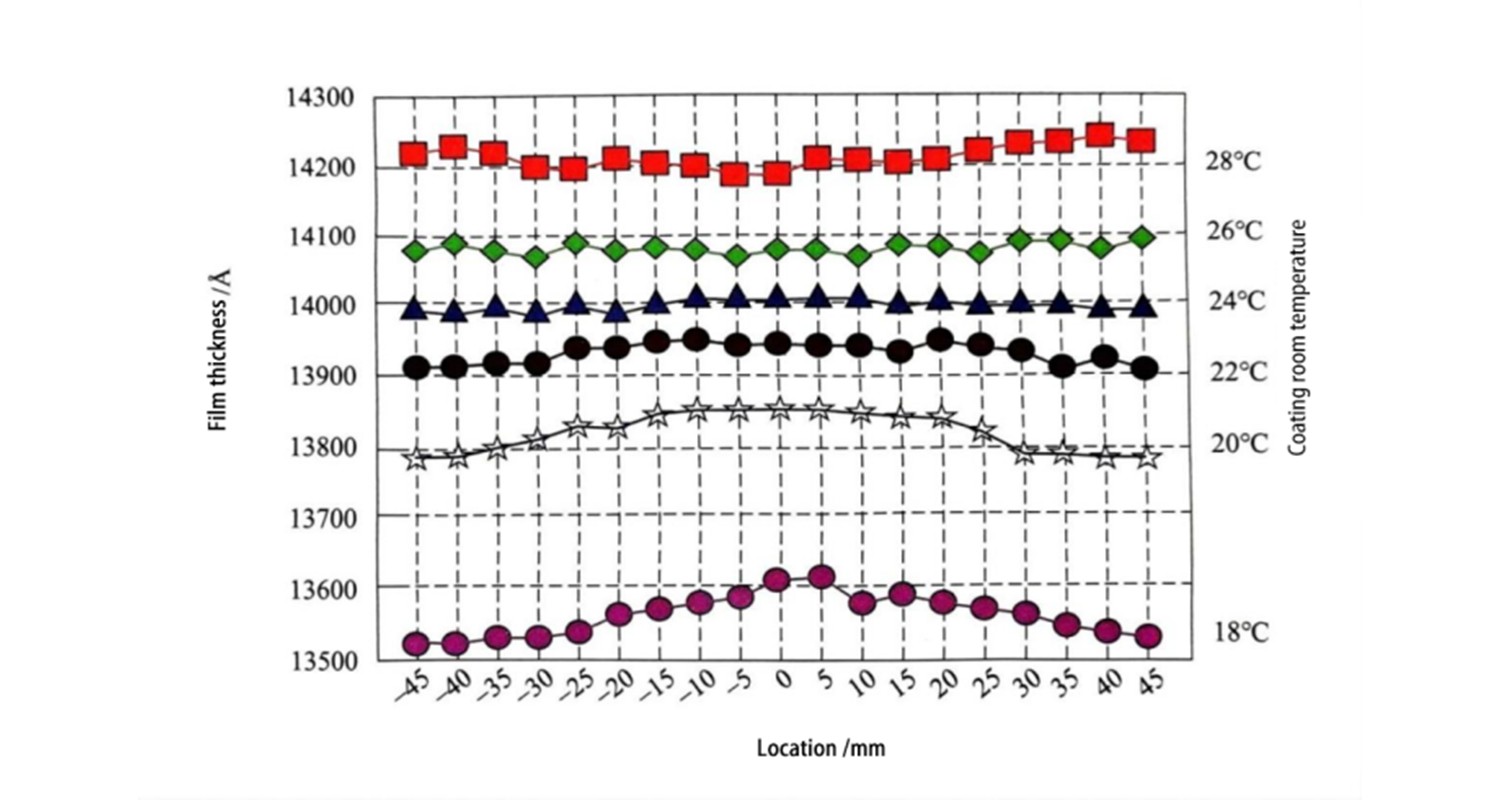
الشكل 5: العلاقة بين درجة الحرارة وتوزيع سماكة الفيلم أثناء الطلاء
تأثير سرعة العادم أثناء الطلاء
ويبين الشكل 6 العلاقة بين سرعة العادم وتوزيع سمك الفيلم. في غياب العادم، يظهر أن مركز الرقاقة يميل إلى التكاثف. زيادة سرعة العادم ستؤدي إلى تحسين التجانس، ولكن إذا تمت زيادتها أكثر من اللازم، فسوف ينخفض التجانس. يمكن ملاحظة أن هناك قيمة مثالية لسرعة العادم.
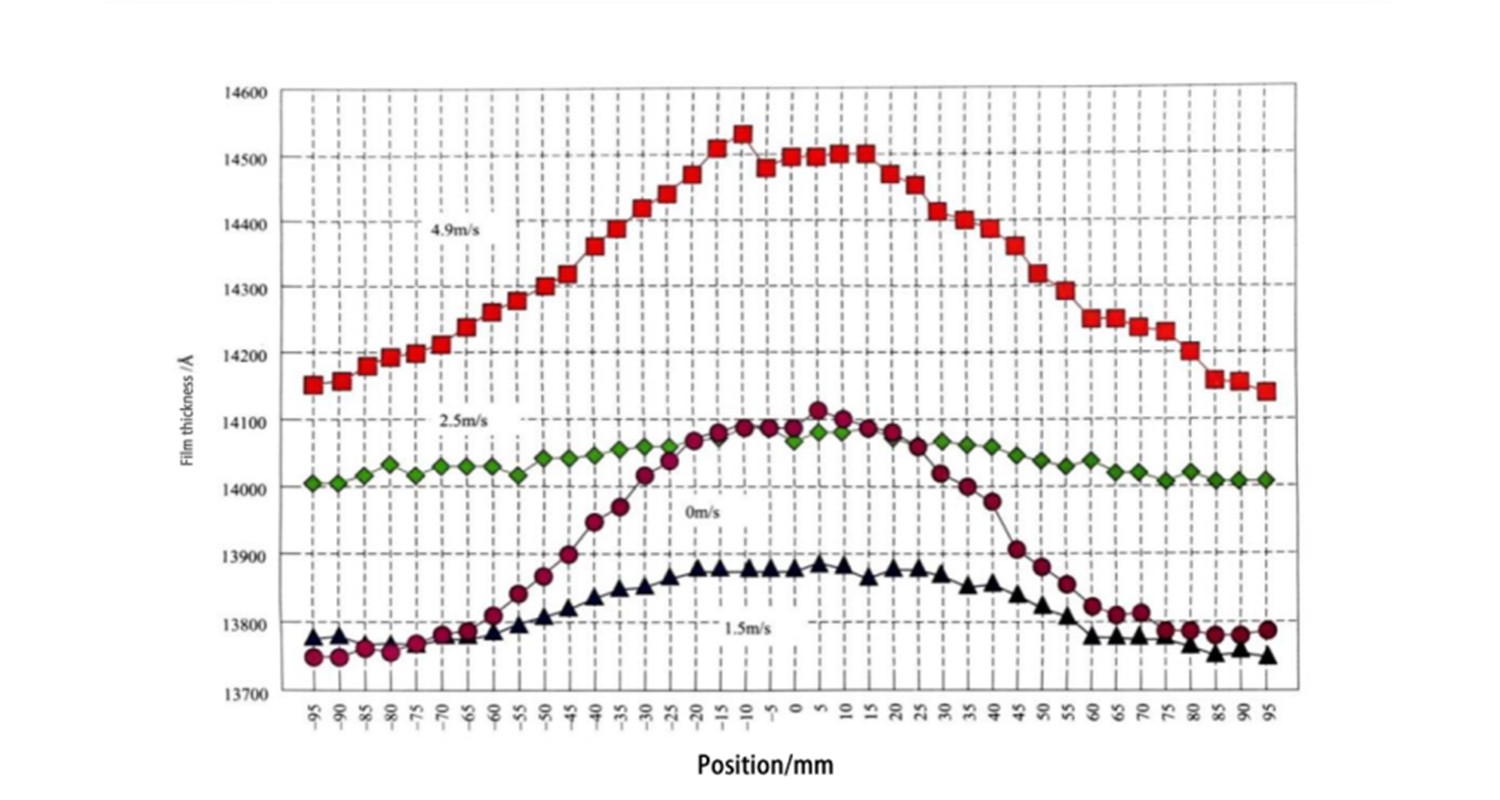
الشكل 6: العلاقة بين سرعة العادم وتوزيع سمك الفيلم
علاج HMDS
من أجل جعل مقاوم الضوء أكثر قابلية للطلاء، يجب معالجة الرقاقة باستخدام سداسي ميثيل ديسيلازان (HMDS). خاصة عندما يتم ربط الرطوبة بسطح طبقة أكسيد Si، يتكون السيلانول، مما يقلل من التصاق مقاوم الضوء. من أجل إزالة الرطوبة وتحلل السيلانول، يتم تسخين الرقاقة عادةً إلى 100-120 درجة مئوية، ويتم إدخال رذاذ HMDS لإحداث تفاعل كيميائي. تظهر آلية التفاعل في الشكل 7. من خلال معالجة HMDS، يصبح السطح المحب للماء بزاوية اتصال صغيرة سطحًا كارهًا للماء بزاوية اتصال كبيرة. يمكن أن يؤدي تسخين الرقاقة إلى الحصول على التصاق أعلى لمقاوم الضوء.
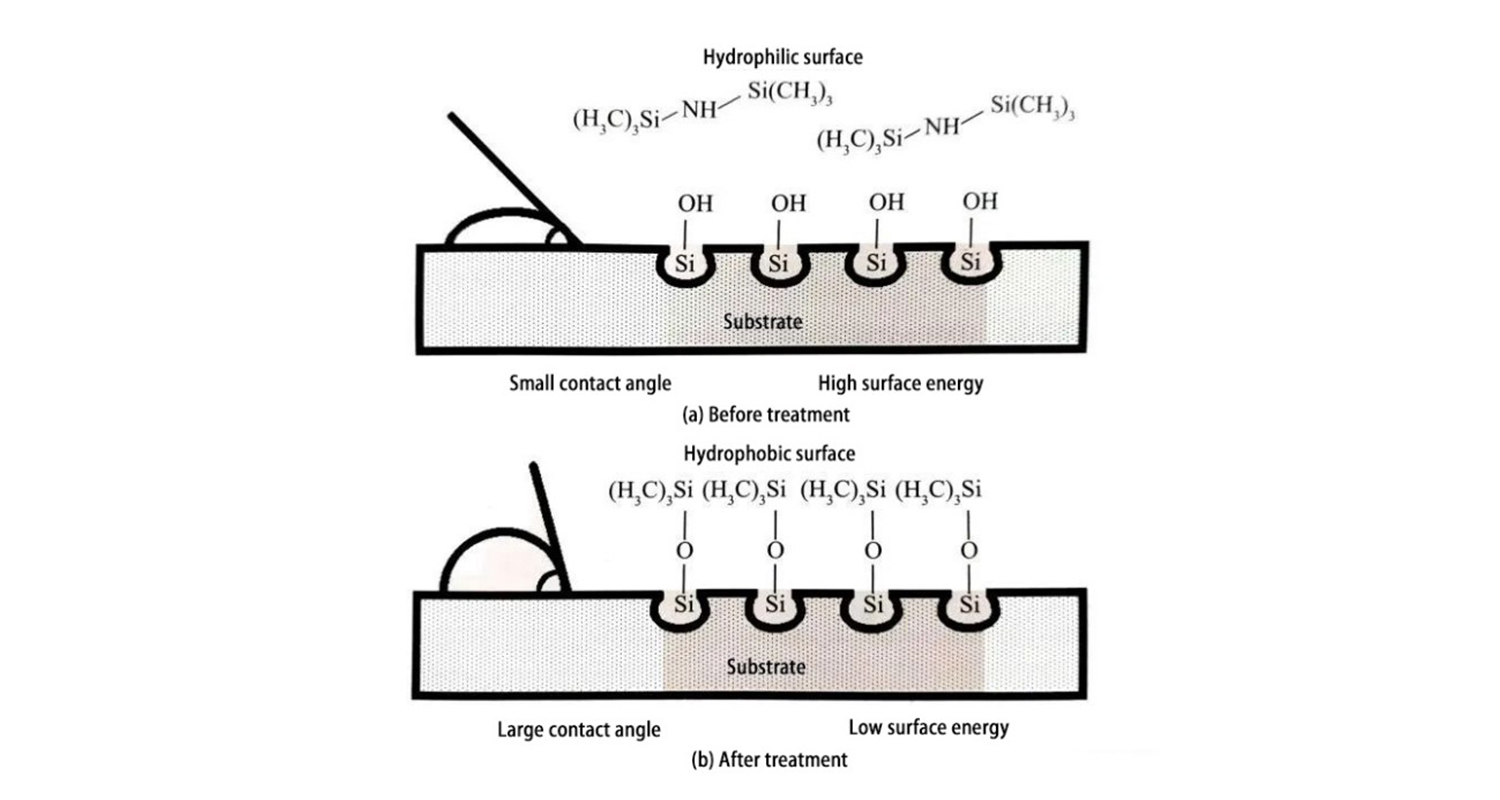
الشكل 7: آلية رد فعل HMDS
يمكن ملاحظة تأثير علاج HMDS عن طريق قياس زاوية التلامس. يوضح الشكل 8 العلاقة بين وقت علاج HMDS وزاوية التلامس (درجة حرارة العلاج 110 درجة مئوية). الركيزة هي Si، ووقت معالجة HMDS أكبر من دقيقة واحدة، وزاوية التلامس أكبر من 80 درجة، وتأثير العلاج مستقر. يوضح الشكل 9 العلاقة بين درجة حرارة معالجة HMDS وزاوية التلامس (وقت المعالجة 60 ثانية). عندما تتجاوز درجة الحرارة 120 درجة مئوية، تنخفض زاوية الاتصال، مما يشير إلى أن HMDS يتحلل بسبب الحرارة. لذلك، عادة ما يتم إجراء المعالجة HMDS عند درجة حرارة 100-110 درجة مئوية.
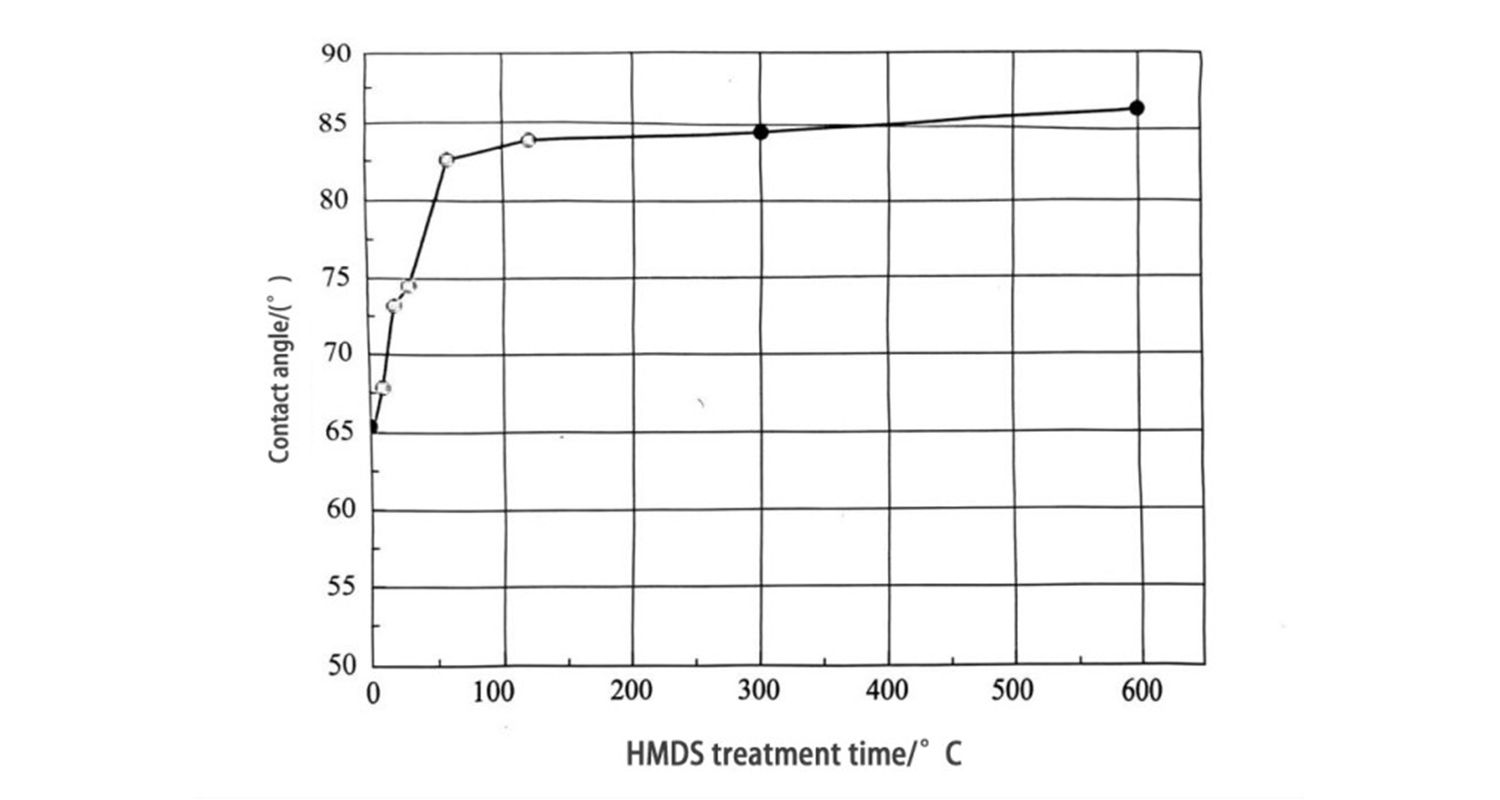
الشكل 8: العلاقة بين وقت علاج HMDS
وزاوية الاتصال (درجة حرارة المعالجة 110 درجة مئوية)
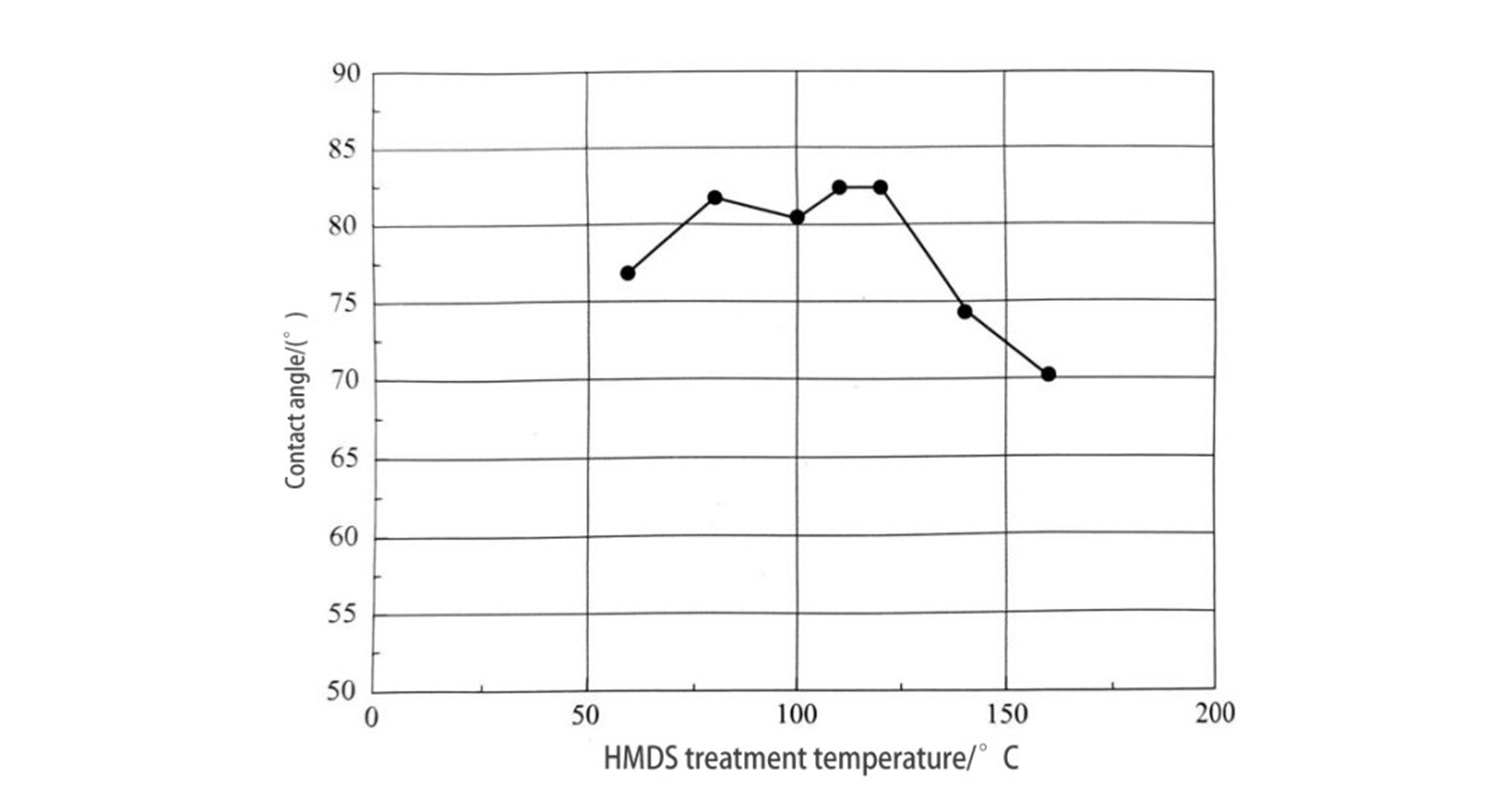
الشكل 9: العلاقة بين درجة حرارة علاج HMDS وزاوية التلامس (وقت العلاج 60 ثانية)
يتم إجراء علاج HMDS على ركيزة من السيليكون مع فيلم أكسيد لتشكيل نمط مقاوم للضوء. يتم بعد ذلك حفر طبقة الأكسيد بحمض الهيدروفلوريك مع إضافة مخزن مؤقت، وقد وجد أنه بعد معالجة HMDS، يمكن الحفاظ على نمط مقاومة الضوء من السقوط. ويبين الشكل 10 تأثير علاج HMDS (حجم النمط هو 1um).
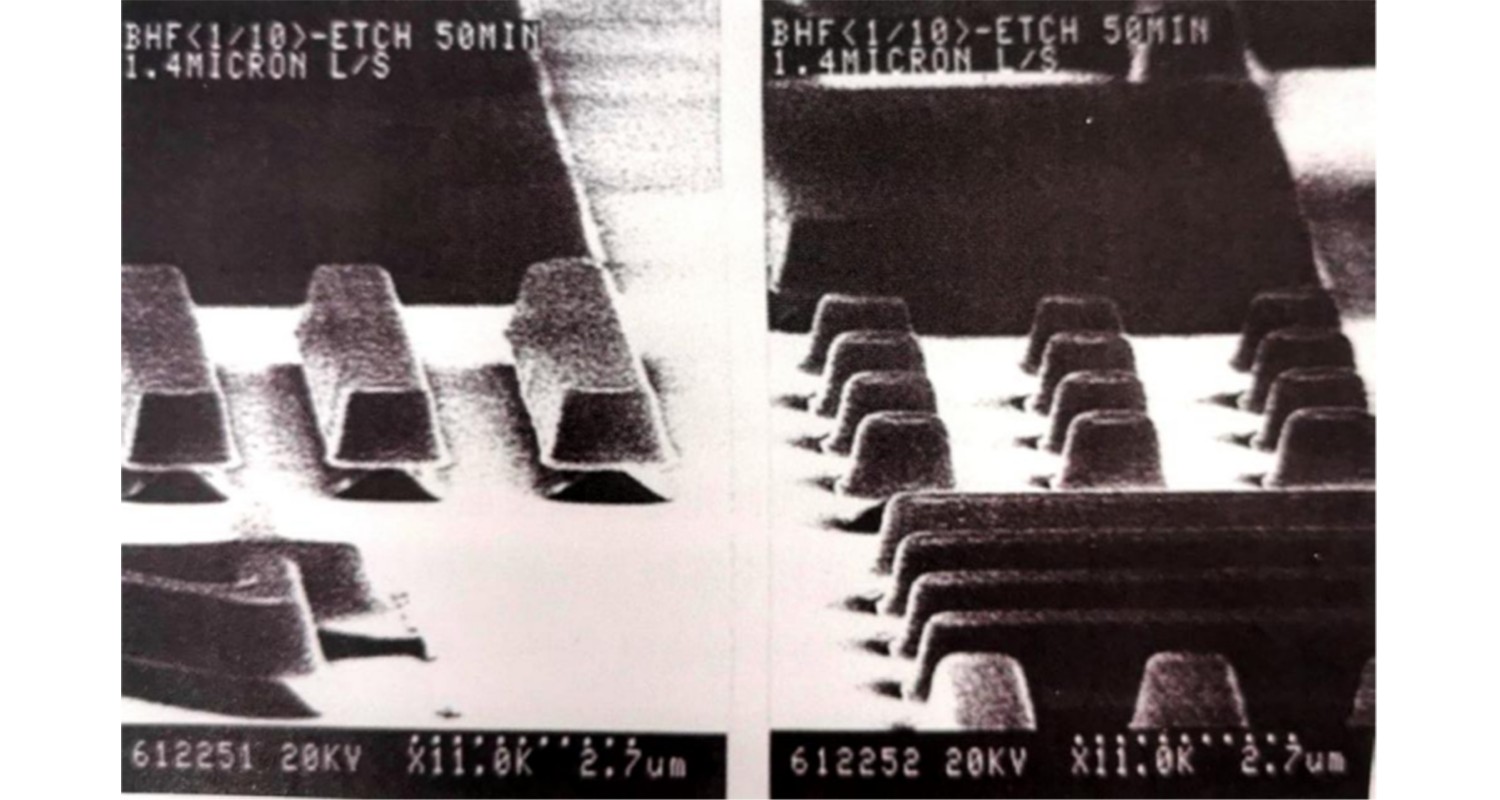
الشكل 10: تأثير علاج HMDS (حجم النموذج هو 1um)
الخبز المسبق
وبنفس سرعة الدوران، كلما ارتفعت درجة حرارة الخبز المسبق، قل سمك الفيلم، مما يشير إلى أنه كلما ارتفعت درجة حرارة الخبز المسبق، زاد تبخر المذيبات، مما أدى إلى سمك طبقة أرق. يوضح الشكل 11 العلاقة بين درجة حرارة ما قبل الخبز والمعلمة A الخاصة بـ Dill. تشير المعلمة A إلى تركيز العامل الحساس للضوء. كما يتبين من الشكل، عندما ترتفع درجة حرارة الخبز المسبق إلى أكثر من 140 درجة مئوية، تنخفض المعلمة A، مما يشير إلى أن العامل الحساس للضوء يتحلل عند درجة حرارة أعلى من ذلك. ويبين الشكل 12 النفاذية الطيفية عند درجات حرارة مختلفة قبل الخبز. عند 160 درجة مئوية و180 درجة مئوية، يمكن ملاحظة زيادة في النفاذية في نطاق الطول الموجي 300-500 نانومتر. وهذا يؤكد أن العامل الحساس يتم خبزه وتحلله عند درجات حرارة عالية. درجة حرارة ما قبل الخبز لها قيمة مثالية، والتي يتم تحديدها من خلال خصائص الضوء والحساسية.
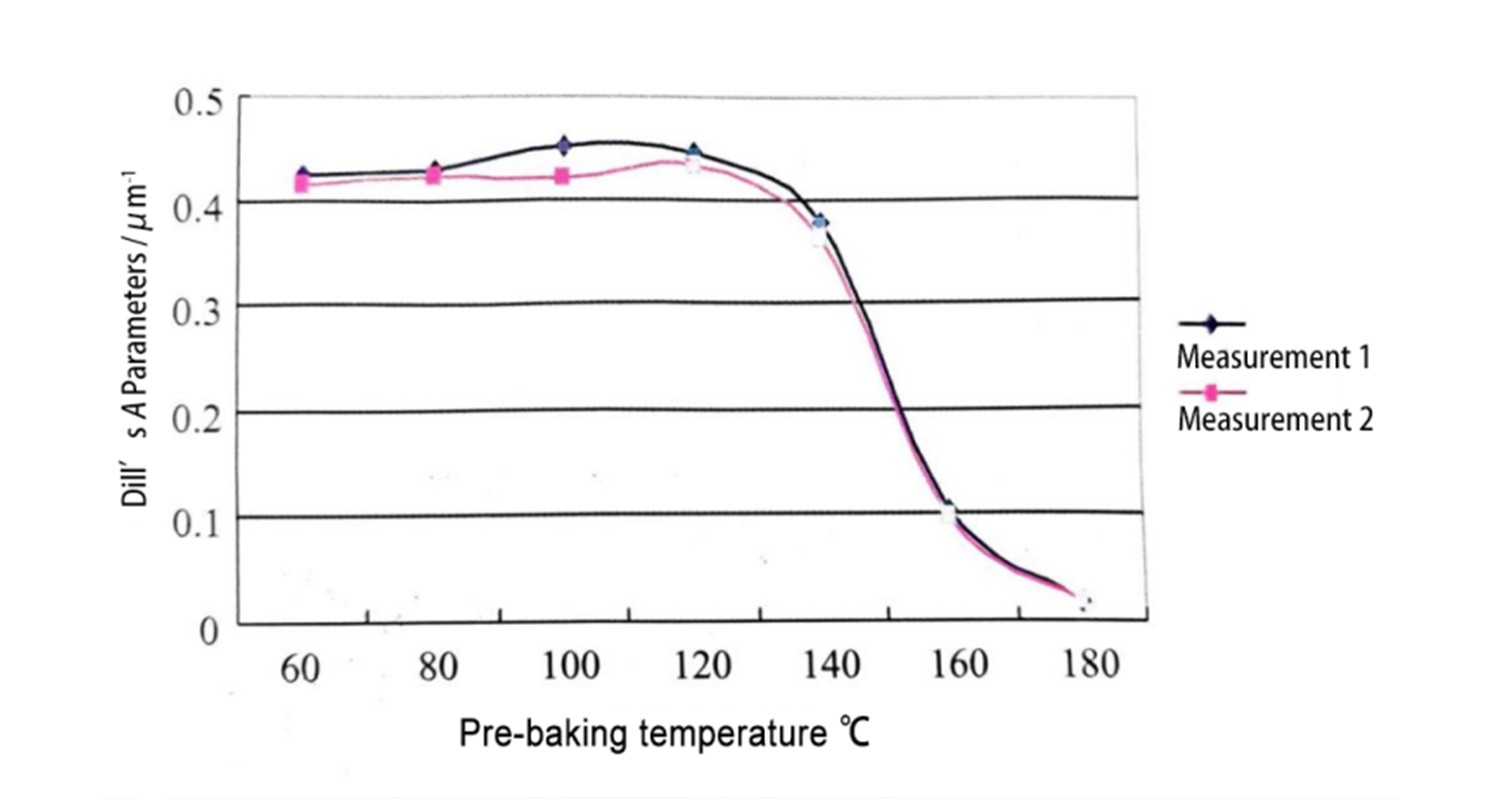
الشكل 11: العلاقة بين درجة حرارة ما قبل الخبز ومعلمة الشبت A
(القيمة المقاسة لـ OFPR-800/2)
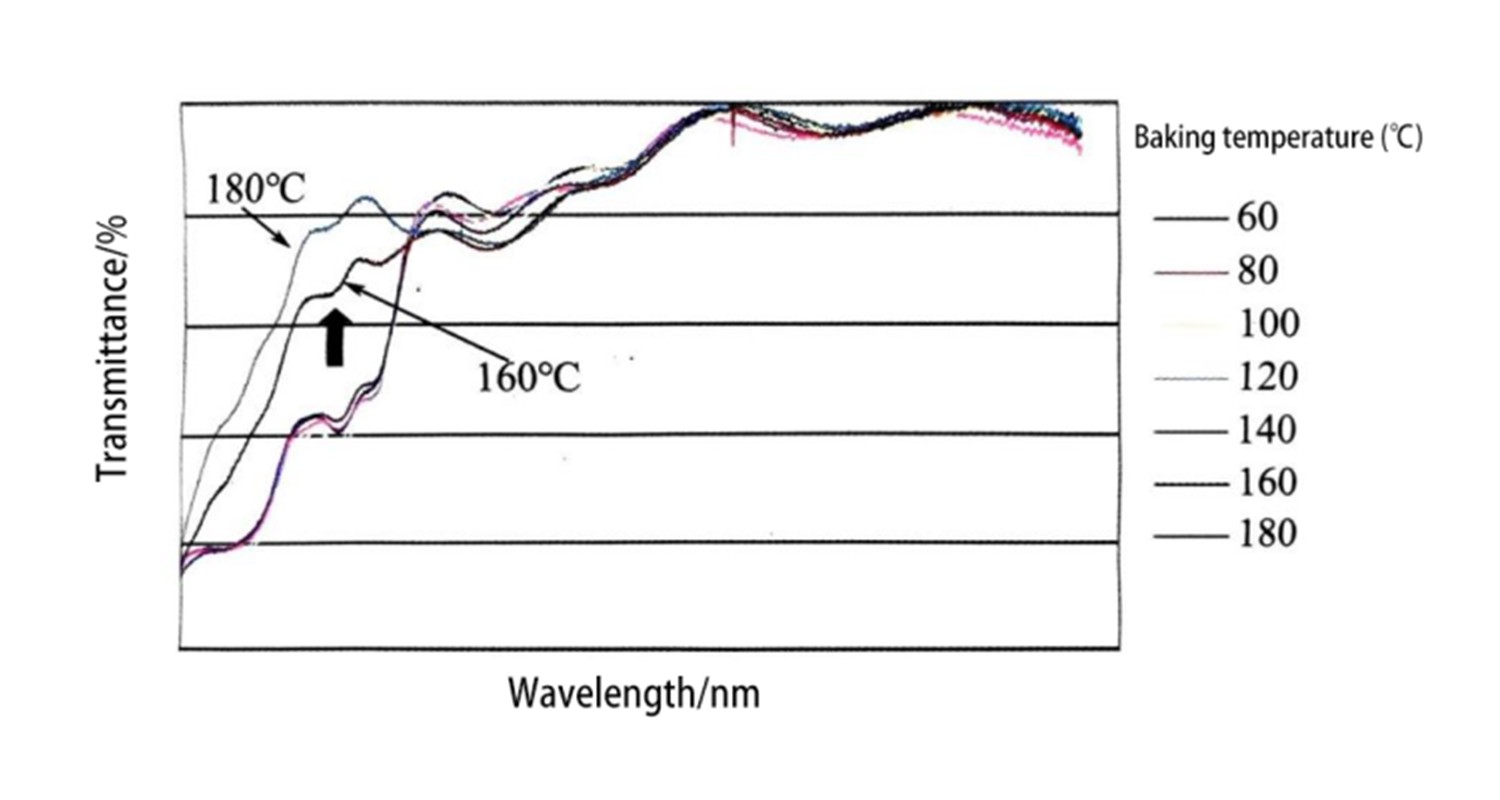
الشكل 12: النفاذية الطيفية عند درجات حرارة مختلفة قبل الخبز
(OFPR-800، سمك الفيلم 1um)
باختصار، تتميز طريقة الطلاء بالدوران بمزايا فريدة مثل التحكم الدقيق في سماكة الفيلم، وأداء التكلفة العالية، وظروف المعالجة المعتدلة، والتشغيل البسيط، لذلك لها تأثيرات كبيرة في تقليل التلوث، وتوفير الطاقة، وتحسين أداء التكلفة. في السنوات الأخيرة، اكتسب الطلاء الدوراني اهتمامًا متزايدًا، وانتشر تطبيقه تدريجيًا إلى مختلف المجالات.
وقت النشر: 27 نوفمبر 2024